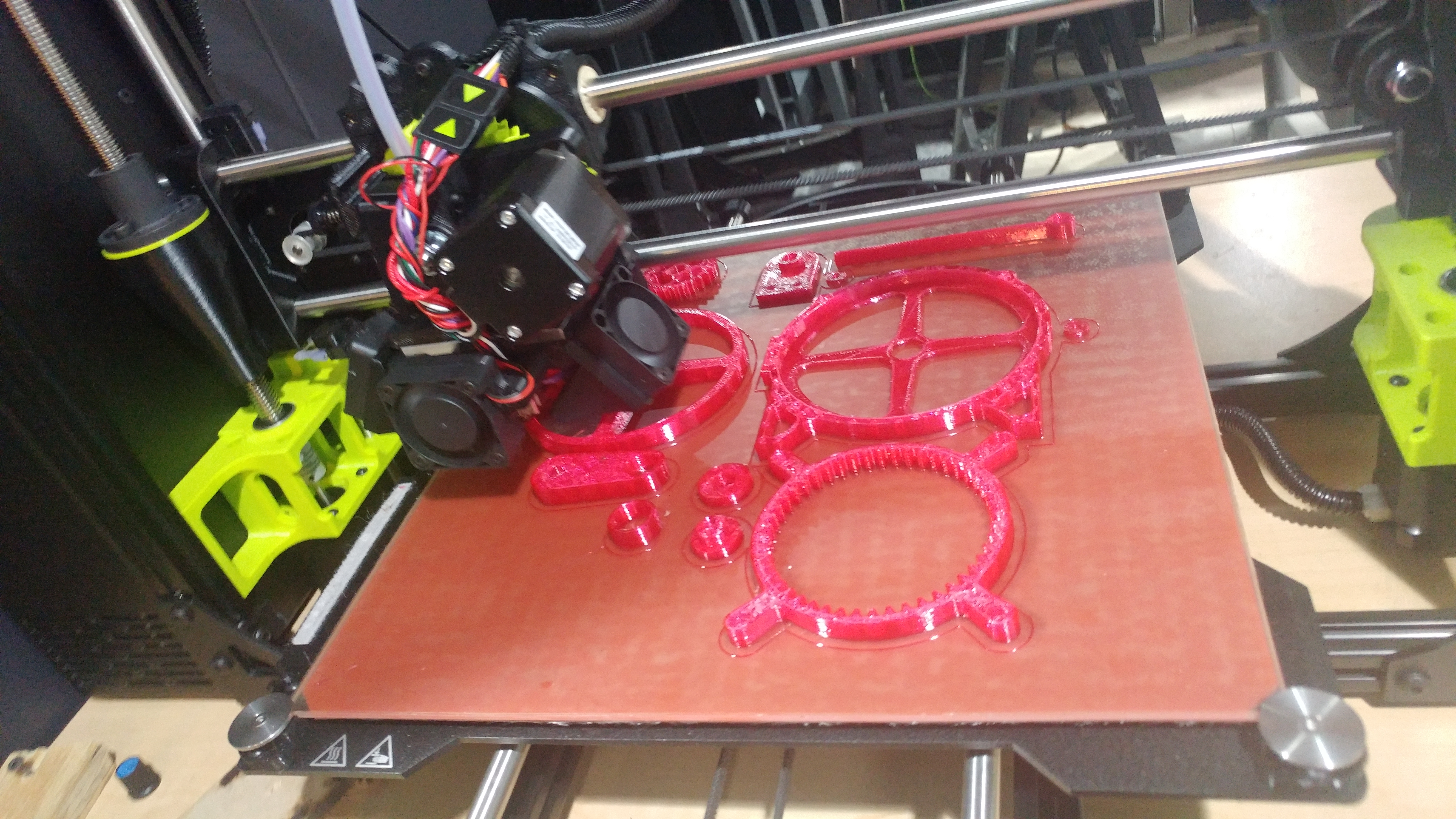
As 3d Printing has been getting more attention, it has gotten difficult to separate reality from the hype. There has been a flood of consumer and commercial grade systems, with the differences in many cases hard to spot. I have spent a great deal of time working with varying materials and printing technologies and have decided to chronicle some of the lessons learned in order to dispel some of the myths, avoid common pitfalls, and set expectations at a realistic level.
The two types of printing that I have been working with are FFF (Fused Filament Fabrication) and SLS (Selective Laser Sintering). Many of you may say “But what about FDM!” FDM is a trademarked term owned by a specific manufacturer of 3d printers. The generic term adopted by many alternative manufacturers for the same technology is FFF. FFF is melted material extruded through a nozzle at high temperature that is fused together layer by layer. This offers a large amount of flexibility in materials and object creation, but has fundamental integrity weaknesses as the layers may split apart (called delamination). The orientation your print may become critical to the structural integrity of your part. SLS uses a material submersed in resin that is burned with a laser across each layer. The bond between layers is indistinguishable and the orientation in no longer as critical. Metal objects may be produced with this process, as well as plastics. Machines using this process are notably higher cost than FFF systems, as is the material and the amount of waste generated.
Most of my time invested has been on FFF systems, as that is at the core of the current market hype. Many manufacturers are trying to push these into the mainstream and get the technology to be as common as your desktop inkjet is today. There are a few who have made the setup and printing process fairly painless, however most of them require quite a bit of tuning and adjustment.
So I’ll skip the any additional comments on types of printers, specific models, and how to choose. There are thousands of those write-ups available all around the internet. Instead I want to take a look at materials available and the strengths and weaknesses in the industrial environment. I’ll start off with some comparisons of materials and generic features, then performance on low end vs high end FFF printers. For these comparisons I have two Cartesian type printers, a QU-BD ThreeUp v3 with E3D v6 hot end and a Lulzbot Taz6 with both a normal single extruder and a Flexy-DuallyStruder v2. For the QU-BD unit, I am using BuildTak sheets, and the Taz6 comes with a PEI surface.
For this post, I will limit my remarks to the common typical materials. I’ll get into polycarbonate, Igus cable tray, and some industry specific filaments later.
Plain PLA
This is the basic cheap easy material to work with. It requires no extra preparation to adhere to most printing surfaces. Is reasonably sturdy, and prints at low temperatures. This is a decent material for fast light duty prints. The layer bonding on this material is decent, but not amazing. While exact specs may differ per manufacturer, I’ll stick with NinjaTek as a baseline.
- Shore Hardness 75D
- Tensile Strength, Yield 7,800PSI
- Elongation at yield 6%
- Integrated stress / strain curve 140in-lbF/in3
- Impact Strength 0.47 ft.lbf/in2
- Abrasion resistance Mass loss 10,000 cycles 0.25g
Source : https://ninjatek.com/wp-content/uploads/2016/05/PLA-TDS.pdf

For industrial use, this material has its primary usefulness in rapid prototype parts and supports. It doesn’t have the impact resistance for functional nest tooling in most cases, or the abrasion resistance for moving components. It does however have a very high tensile strength (even higher than ABS) which makes it suitable for many applications where broad force is applied. It also taps well and holds threaded inserts with ease.
- Prototype product for fitment and early production equipment testing
- NC cut nesting details adjusted to customer product before prototype runs
- Alignment checking. Cosmetic details and covers
Nothing taking any abrasion, or impact. Overall, if you are looking for parts to actually use on an end effector, nest, or part locator, just move on.
PLA With Additives
This is where PLA gets confusing. It is incredibly common to see PLA blended with other materials, from wood fiber to stainless steel. You can even get magnetic iron, conductive, and carbon fiber. While these may sound intriguing, pay attention to the fact that these do not significantly add a large amount of structural strength to the material. Printing with aluminum may give you a part that can be polished to a shine, but the PLA component of the layers still peels apart just as easily. The carbon fiber material is notably stronger, however if you don’t have a hardened steel hot end and nozzle, this will wear down the components of your printer rapidly. I have yet to compare carbon fiber and Nylon Alloy 910 directly, however at the moment I can’t recommend carbon fiber for durable prints due to the potential for machine damage with long term use.

Bottom line here, unless you need a specific property, such as conductive or magnetic, these are best ignored for industrial use. While they have some nice cosmetic properties for the typical user, they rarely have any impact on practical use.
ABS
This is the most commonly used, the workhorse of 3d printing materials. It was the first mass marketed material with a decent amount of strength to it.
- Shore Hardness 70D
- Tensile Strength, Yield 5,100PSI
- Elongation at yield 8%
- Integrated stress / strain curve 160in-lbF/in3
- Impact Strength 4.94 ft.lbf/in2
- Abrasion resistance Mass loss 10,000 cycles 0.10g
Source : https://ninjatek.com/wp-content/uploads/2016/05/ABS-TDS.pdf
With the impact resistance so much greater than PLA (10x), this material could be used for light duty nests and surfacing support details with ease.

ABS is a bit trickier to work with than PLA. It has a shrinkage percentage to keep in mind for dimensional accuracy. It won’t adhere to a non-heated printing surface, and tends to warp or delaminate easily when not printed in a temperature controlled environment or enclosed printer. Even with a print surface at 110deg C, it still requires additional prep to adhere. Either a PEI surface, kapton tape, or an ABS slurry (ABS dissolved in acetone to make a glue paste for your print surface) are a requirement. Even then tall prints with a small surface contact area may still tend to break away mid print. Another concern is the fumes it emits are considered to by carcinogenic. The work area and printer should be well ventilated and you shouldn’t sit over it for long prints.
Another thing to consider is post processing. Since ABS is dissolvable by acetone, there are many techniques for smoothing the surface or welding larger components together with acetone. When acetone smoothed, the adhesion between layers is far greater than when initially printed. They have essentially been chemically bonded at that point. The down side to consider is the process is difficult to control dimensionally and there is risk of melting small geometry on the part.
Bottom line, if you have a printer and environment an capable of working with it, this is a solid durable material for typical uses. I’d recommend it for surfaced part backup nests, holding fixtures, and anywhere a basic solid material is required but a high strength material isn’t required or cost efficient. Keep in mind this is slowly being replaced with Nylon and Polycarbonate alloys as the price on those comes down, however we will discuss these more in the advanced materials topics.
PETG
This material is a bit newer, and sits solidly in between ABS and PLA. On the home use front, it has been rapidly replacing ABS as the material of choice. Its recyclable, generally considered food safe, and typically will not warp or shrink. While exact specs differ greatly, and the above referenced manufacturer does not offer PETG, a few generic specs can be obtained.
- Rockwell R Hardness 106-120 (somewhere around 100-110 Shore D)
- Tensile Strength, Yield 7,110-7,687PSI
- Elongation at yield 4%
- Impact Strength 1.5-1.84 ft.lbf/in2
Source : http://www.makeitfrom.com/material-properties/Glycol-Modified-Polyethylene-Terephthalate-PETG-PET-G
Source : http://www.matweb.com/search/datasheet.aspx?matguid=9aecd2bc30384b5a96af1263ba5a27d7&ckck=1

One property not defined on any datasheet I could find is abrasion resistance. This material holds up to movement quite well. I made some light weight gears out of this with a rotary to linear actuator and have been pleasantly surprised to see how well it holds up. The layer adhesion is better than PLA and it is notably stronger. It’s not quite as impact resistant as ABS however, and the post processing capabilities are also lost. I could see utilizing this in the industrial space for handles and light friction guards, and guides; however this material generally fails to find a niche in practical applications for a typical industrial environment.
Stay tuned for the next article, where I will be evaluating Alloy 910, Nylons, TPU, TPE and PolyCarbonate.